Method Statement for Casting Sequence - Short Line Pier Segment
1. INTRODUCTION
1.1 PURPOSE OF THE DOCUMENT
The purpose of this procedure is to outline the sequence of operations to be carried out for casting pier segment using the Short Line method, and ensure that all works will be conducted safely in accordance with the drawings and the project specifications.
1.2 PROJECT DESCRIPTION
Ho Chi Minh City Urban Railway Construction Project – Ben Thanh – Suoi Tien section (Line 1), contract Package 2 consists of approximately 12 km long of elevated viaduct structures, erected by span-by-span Method. All activities related to the construction of reinforced concrete precast segments will be carried out in the precast yard, located in Road 11, Long Binh Ward, District 9 (HCMC) as per layout on figure 1.
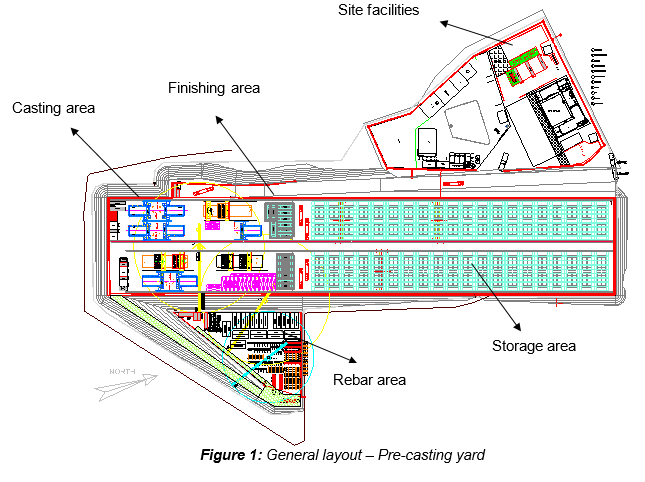
1.3 SCOPE OF WORK
This procedure is developed for the casting sequence of pier segments, produced with the short line casting method for both type of span: straight and curved.
1.4 REFERENCES
All reference documents are intended to refer to the last issued revision.
- Specifications:
- Clause 12.4.1 “Precast segment casting” Section 12-3 of 19 from Outline construction specification – Package 2: Civil (Elevated & Depot)
- “Standard specification for concrete structures – 2007, Materials and construction” from Japan Society of Civil Engineers, regarding the stripping strength (14MPa) required to reach.
- Method Statement:
- HCMC-261-CSYD-CWS-MST-00012 “General precasting works at precasting yard”
- HCMC-261-CSYD-CWS-MST-00040 “Precast segment production – Short Line Pier mould”
1.5 DEFINITIONS
All relevant definitions have been given in Section 1.5 “Definitions” of the Method Statement “General precasting works at precasting yard” HCMC-261-CSYD-CWS-MST-00012 and “Precast segment production for Short Line Pier mould” HCMC-261-CSYD-CWS-MST-00040
2. SAFETY & ENVIRONMENTAL RISKS
All the Hazard Analysis & Risk Assessment, Tools & Equipment and Emergency response, regarding each task described in this procedure, such as: casting of segment, segment lifting, operations & preparations of the mould, etc. will be carried in each related method statement. Refer to Section 1.4 “References” for further details.
3. CONSTRUCTION RESOURCES
All the construction resources, such as personnel, plant & tools and materials regarding will be described in each related method statement.
4. SHORT LINE PIER MOULD – SLP
4.1 DESCRIPTION
Listing of mould for the production of pier segments:
- Short Line Pier #1 (SLP #1)
- Short Line Pier #2 (SLP #2)
- Short Line Pier #3 (SLP #3)
- Short Line Pier #4 (SLP #4)
4.2 COMPONENTS
Each Short Line Pier mould has the following components:
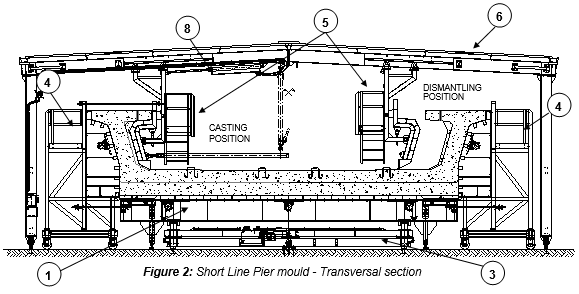
1. Soffit table (typical segment) | 1 Nos |
2. Soffit table (pier segment) | 2 Nos |
3. Manipulator with 4 hydraulic vertical & horizontal jacks | 1 Nos |
4. External side forms (left & right) | 1 Set |
5. Inner forms (left & right) | 1 Set |
6. Portal frame for inner forms (including the roof) | 1 Set |
7. Fixed bulkhead (with supports, Stairs & platforms) | 1 Nos |
8. Hydraulic system (for inner forms) | 1 Set |
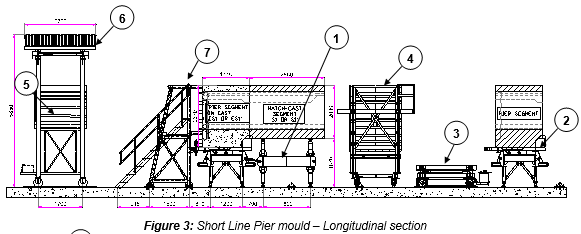
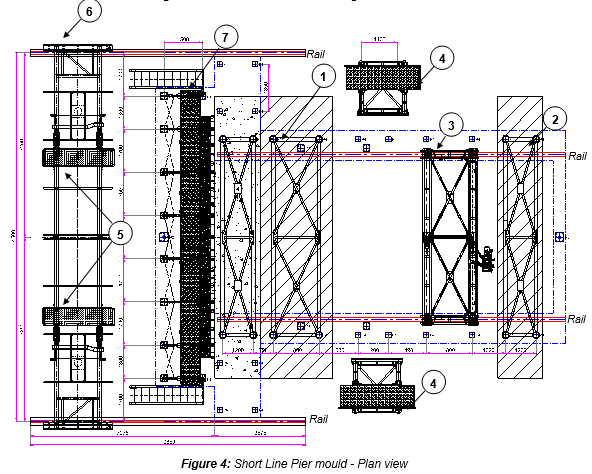
5. CONSTRUCTION SEQUENCE
5.1 INTRODUCTION
In the precasting yard, each span (straight or curved) is built by assembling differents segments of variable longitudinal lengths. More than 4,587 segments shall be manufactured by Match-Cast (M/C) principle with combination of short line and long line casting method.
Straight spans will be cast with the long line casting method, via the Long Line Typical mould (LLT), while curved spans will be achieved using the short line casting method via the Short Line Typical mould (SLT). Casting of pier segments for straight & curved spans will be achived on dedicated Short Line Pier mould (SLP), using the short line casting method.
Segments are match-cast. It means that the previously segment, after being cast, is defined as counter mould segment (Match-Cast); the new segment will be cast against, ensuring a perfect and unique connection match-cast face.
After the pier segment (ES1 or ES1’) has been cast, and the stripping concrete strength (14MPa) reached, the elements of the mould shall be stripped and shifted. The segment S1 or S1’ used as M/C segment is shifted on the rail track by means of manipulator and removed from Short Line Pier mould to finishing area using the 50ton gantry crane. The soffit table for S1 is then lifted aside.
The cast pier segment ES1 or ES1’ is moved on the rail track by means of manipulator to the lifting position. It is not lifted until the concrete strength is reached. Finally a “free” space is created to start a new casting pier cycle. All succeeding pier segments “ES1 or ES1’“ shall be cast against previously “S1” or “ S1’ “ transferred from other mould areas.
5.2 MOULD OPERATION CYCLE FOR SHORT LINE PIER SEGMENT
- Survey of as-built geometry.
- Confirmation of as-built data within tolerance
- Confirmation of demoulding strength
- Remove inflatable tubes (also called “satujo”)
- Remove anchorage bolts
- Strip inner forms & shift portal frame on rail behind the fixed bulkhead
- In parallel, marking of segment (ID number, Span No, date of casting & arrow). Refer to the method statement “Segment marking” HCMC-261-CSYD-CWS-MST-00022
- Lower / strip & shift external side forms
- Break bond between cast segment ES1 (or ES1’) and Match Cast (M/C) typical segment S1 (or S1’)
- Move M/C typical segment S1 (or S1’) to lifting position
- In parallel, lift M/C typical segment S1 (or S1’) to finishing area
- Break bond between cast segment ES1 (or ES1’) and fixed bulkhead
- Move cast segment ES1 (or ES1’) to lifting position but don’t lift.
- Lift soffit table for pier segment ES1 (or ES1’) to be cast (placing 300mm away from fixed bulkhead)
- Lift soffit table for typical segment S1 (or S1’) to 300mm away from match-cast position
- Clean external side forms & apply the mould release agent (mould oil)
- Clean inner forms & apply the mould release agent (mould oil)
- Adjust bearing downstand at ES1 (or ES1’) soffit table including restrainer recess
- Bolt anchorages to fixed bulkhead
- Place the pre-checked rebar cage on soffit table for pier segment ES1 (or ES1’)
- Shift soffit table for pier segment ES1 (or ES1’) with rebar cage to cast position
- Lift typical segment S1 (or S1’) to soffit table for match-cast
- Apply debonding agent to match-cast segment face
- Shift M/C typical segment S1 (or S1’) to match-cast position
- Position & pre-close the external side forms
- Connect PT duct to anchorages, bursting reinforcement, align PT duct with supports including inserts at bottom slab and webs
- Inspection with SCC/GS prior to inner forms closure
- Shift on rail the portal frame to casting position & install inner forms
- Install inserts at top flange of segment (Survey plates, inserts for handrails, others..)
- Final closure of mould
- Final survey Refer to the method statement “Geometry control for short line casting method” HCMC-261-CWS-MST-00016
- Inflate “Satujo”
- Final inspection before casting / Cleaning of workstation
- Cast pier segment & concrete finishing (floating) Refer to the method statement “Segment concreting works” HCMC-261-CWS-MST-00020
- Cure pier segment Refer to the method statement “Curing of segments” HCMC-261-CWS-MST-00021
- Transfer cured segment to finishing area, after lifting strength concrete required reached Refer to the method statement “Segment liftings & handling works” HCMC-261-CWS-MST-00023
- Segment finishing works Refer to the method statement “Segment finishing works” HCMC-261-CWS-MST-00024
- Remedial works for segment (if needed) Refer to the method statement “Segment remedial works” HCMC-261-CWS-MST-00025
- Storage of segment Refer to the method statement “Segment storage and stacking” HCMC-261-CWS-MST-00026
- Load segment on trailers for site delivery
Refer to the method statement “Segment delivery and transportation” HCMC-261-CWS-MST-00027 Note that all mould preparation and operations for pier segment (“ES1” and “ES1’ “) mentioned in this cycle will be described in the dedicated method statement “Precast segment production – Short Line Pier mould” HCMC-261-CWS-MST-00040.
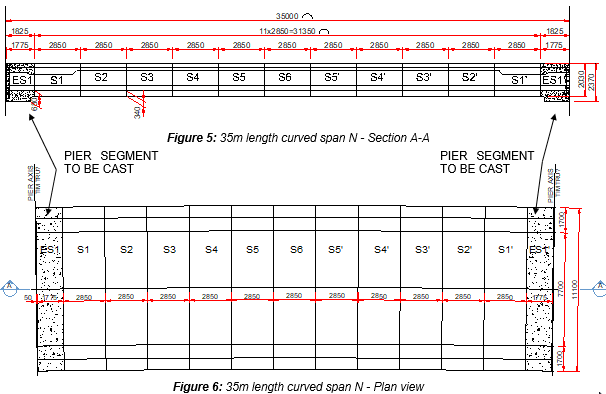
Note that typical segments (“S1, S2, S3, S4, S5, S6, S5’, S4’, S3’, S2’ and S1’ “) are always cast at dedicated mould (SLT or LLT). For further details, refer to the following method Statements:
- “Casting sequence for short line typical segment” HCMC-261-CWS-MST-00017
- “Precast segment production – Short line typical mould” HCMC-261-CWS-MST-00015
- “Casting sequence for long line typical segment” HCMC-261-CWS-MST-00019
- “Precast segment production – Long line typical mould” HCMC-261-CWS-MST-00041
5.3 SEGMENT PRODUCTION – DAILY CYCLE
The following sub-sections outline the process which typically accomplishes the pier segment production cycle of in hourly basis, with the Short Line Pier mould.
5.4 CONCLUSION
The Short Line Pier (SLP) mould, used to cast pier segment for straight and curved spans, can manufacture 1 pier segment / 2 days, in accordance with all safety and quality requirements.
6. ACTIVITY HOLD POINTS
All Activity hold points will be identified in the Inspection & Test Plan (ITP).
7. INSPECTION & RECORDS
All Inspection / Check-lists & documents records will be identified in the Inspection & Test Plan (ITP).